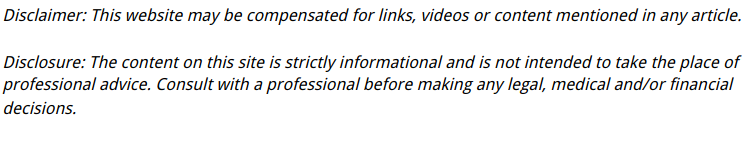
Many industries today make use of air compressors of one sort or another, and these systems involve canisters of such air, along with air compressor piping and tubes and air fittings and clamps if need be. Compressed air distribution can save a lot of work for today’s hobby enthusiasts and factory workers alike, such as a compressed air systems for wood working. A compressed air systems for wood working might be used at a factory, or even in a privately owned, small wood working shop at one’s own residence. There are good reason to use a compressed air systems for wood working or for other work, and such air can clear out debris, cool down surfaces, or move other materials onto surfaces in a desired manner. What is there to know about a compressed air systems for wood working, or using air pressure in other industries?
For Wood Working
Wood is one of the earliest materials used for construction, whether for boats, weapons or tools, or living arrangements. This is still true today, as plastic and metal have not replaced all applications for wood. The construction industry makes generous use of wood for building homes or hardwood floors, for example, and a lot of furniture is made out of wood (and not just by the Amish). Wood is also useful for many tools and small boats today, and these wooden items are made both in factories and in private wood shops for recreational wood working. Many Americans have their very own wood workshop on their property, where they might built just about anything. Many tools and supplies are used there, from band saws to hammers to glues and nails. Compressed air plays a role here, too.
What can compressed air do for a wood working shop? Air does more than cool a person down when vented through a system, and a compressed air systems for wood working is hardly an air conditioner. Instead, a wood worker may set up pipes and nozzles for air compressors over their work benches and other areas, anchored to the ceiling for convenience. Placing these pipes on the floor is possible, but that could result in a tripping hazard. Once a wood worker has all the pipes and nozzles set up over their work area, they may connect it all to compressed air tanks and motors to pump it. Why might such air be used? Wood working is known for generating a lot of wood scraps, sawdust, and other fine particles during work, and all of this may be a time-consuming hassle to clean up on a project. Rather, these compressed air systems can be turned on, and they will blow the particles off of the table and finished wooden items and onto the floor instead, cleanly and easily. This imposed no risk to the wooden items, either, since no chemicals or blunt force are being used. Once all of these wood scrap and particles are on the floor, the wood shop owner may then simply sweep them up and dispose of them as usual.
Air Systems Elsewhere
It is clear that compressed air blowers are useful for clearing off wooden sawdust or scraps, but compressed air is capable of more. Such devices may be found in car factories as well, and other shops where metal items are being made. Here too, the air compressors may be set up on the ceiling for convenience, or they may be mounted on robotic arms or poles to keep them clear of workers’ space. They may blow off metal scraps and dust left over when a piece of metal has been drilled or cut, for example, clearing the finished material of any debris. Meanwhile, compressed air systems may be quite useful for spraying liquids onto finished surfaces, such as car body paint. Such paint is not applied with a regular paint brush; rather, compressed air nozzles will use mix that air with car paint and spray it onto the intended surface. Such devices may be handheld for factory workers, or even be mounted on robotic arms for large scale jobs. Even spray foam chemicals for wall and attic insulation are applied this way, since spray foam is not merely painted on. Air pressure applies that foam.