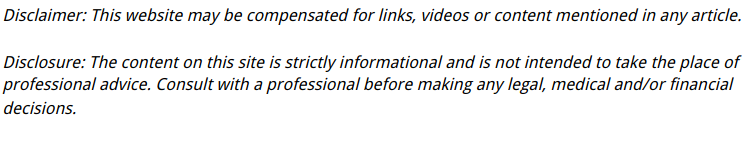
Air compressor systems are a vital piece of all manufacturers in the United States, no matter the industry. Therefore, air compressor pipes, as well as other parts and maintenance, of the air compression business is quite large. With the need for air compression systems in about 70% of all American manufacturers, service and maintenance are continually necessary.
Air Compressors for Both Electricity and Heat
Air compressor systems are often the generators of a significant amount of electricity for any manufacturer, with as much as 90% of that power generating heat as well. Considering the vast amount of heat that runs through compressor systems air compressor pipes and the wear they face must be considered. Along with the service of the systems, replacement of air compressor pipes and other parts is likely on a regular basis.
However, it is important to know that with even 10% of pressure loss can increase costs by over one full percent. For this reason, to make sure that expenses remain low, and productivity complete, full service and maintenance of the air compression system should be considered at all times.
Manufacturers and Other Businesses Working with Air Compression
While air compression is used in a manufacturing warehouse, it is also important in the auto repair industry. Both in the tools used by mechanics, there are compressed air systems for auto body construction and compressed air systems for auto repair. They involve both the management of the shop as well as powering the tools that will repair the vehicles. With the ability of compressed air systems to hold heavy equipment they lift for automobiles make it easier for the mechanics in these shops to get to the interior of the auto systems where repairs need to be made.
Value of the Compressed Air System
There are some facts to consider when maintaining the air compressor system for any business, especially with the need for productivity to keep up with your work. Some of these factors include:
- A properly designed system will recover between 50% and 90% of the heat it generates
- About 50,000 British thermal units per hour are available for the capacity of a unit running at full load
- Without an air receiver tank, a buffer can be a temporary solution, but maintenance or service could bring this addition at the same size of the compressor to run at full load
- Taking in the cooler air requires less energy to produce the necessary energy
There are many ways to help keep the full productivity of your air compressor system. Managing some of these steps on your means that fewer part replacements will be needed in the long run, along with minimal scheduled service.