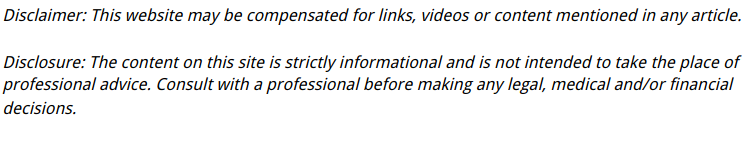
Overall, the automotive restoration industry is a solid one. As long as people drive cars, someone will need a car body repair shop. Some people will want to get fast collision repairs. Car accidents have existed for as long as the vehicles themselves have existed. Of course, when people are looking for ‘vehicle body paint shops near me’ online, they won’t necessarily be looking for automotive accident repairs. They might just want auto paint works for the sake of changing the look of the car.
There are many ways to make an automotive business like this more accessible for the people who plan on using it frequently. Some people will only go to auto shops once or twice yearly. Convenience will always be important to automobile customers. Today, there are body shops with loaner cars. Many customers like them, since they might be driving to the shop in the only car that they have.
A loaner car will give them the reliable transportation that they need to leave the business at all. There might be situations where it will actually be relatively cheap to use the store’s loaner car. Using ride-sharing services can be expensive, especially for individuals who live far away from the business in question.
You only get the best services from your automobile by paying attention to its repair and maintenance needs. Auto body repair and maintenance needs are among the many things you should be keen on in your car. With unpredictable weather conditions and other damage, the chances of your auto body wearing off are higher. You can, however, handle this by finding an auto body and mechanical repair shop near you.
While you might have options on the market, ensure you select a shop that provides auto body and glass repair and maintenance services. You should also be keen on other services that might make your automobile remain functional and productive for a long time. Understand that paintless dent services are vital in the restoration process. Look for a paintless dent repair near me for effective restoration services if your automobile needs it.
Consider other options when you find a shop where an auto body painter needed extra help to provide the best services. You need a shop with experts and mechanics that can provide your automobile with the services it needs to maintain high performance and functionality. As you check the auto body restoration shops near me, ask about the services and the professionals that provide them. Ensure you assess their qualifications and experience level before proceeding with your plans.
You want to set up your own auto body shop this year. How can you set things up so that you’re saving money, even as you expend energy?
Figuring out your air compressor isn’t a bad place to start. Air compressor piping still eludes many professionals today, due in no small part to their need for constant maintenance. You can end up doing everything right and still lose money if your compressed air fittings aren’t synced properly. Before you take on a new project, consider reading the list below. Your air fittings are in no doubt in need of a critical eye.
A few tweaks and a few notes can save you hundreds of dollars every year.
Defining The Compressed Air System
Let’s start off with the basics. Nearly 70% of all manufacturers today have a compressed air system in place. Energy audits conducted by our very own U.S. Department Of energy (or DOE) suggested over 50% of compressed air systems at small and medium-sized facilities have low-cost energy conservation opportunities. This is great news for anyone just getting started in the auto body or hobbyist car kit industry. There’s money to be saved, if you know where to look.
The Cost Of Compressed Air Leaks
Here’s one area you should keep a close eye on. Air compressor leaks are more than just frustrating. They can be an incredibly costly issue that sets you back and keeps your projects on the backburner. A recent study found a mere one-eighth inch diameter hole in a 100 psi system can cost you more than $1,200 in wasted energy. It’s worth a few hours of maintenance time to keep these leaks manageable and your wallet in the green.
Checking Your Pressure
Don’t forget to double-check your pressure, too. Pressure loss in a properly designed system will be less than 10% of the compressor’s discharge, which can be found on a gage on the outlet of the compressor. Pressure loss greater than 10% should have you evaluating your distribution system and identifying the areas causing excessive pressure drops. A good rule-of-thumb is every two pounds-per-square inch decrease will reduce your operating costs by nearly 2%.
Saving On Energy
The goal is to save on energy. Anything less and you’re working yourself to the bone unnecessarily. As much as 80% to 90% of the electrical energy used in an air compressor is converted to heat, with a properly designed heat recovery unit able to take back at least 50% of this heat for heating air. Around 50,000 British thermal units (or Btus) per hour should be available for every 100 cfm of compressor capacity. You’ll learn these numbers slowly, but surely, as you get the hang of your own unique process.
Using The Right Air Compressors For Your Shop
It’s time to figure out your compressed air piping design. If your compressed air system doesn’t have an air receiver tank in place, it’s suggested you add one to buffer short-term demand changes. This will also reduce the on/off cycling of the compressor, which can become overworked easily. The tank should be sized to the power of the compressor, such as having a 50 hp air compressor with a 50-gallon air receiver tank. This logic will stick after a little practice.
Save energy. Save time. Double-check your air compressor tubing this year and get off on the right foot.